PROCESSSCISSORS
Laser cutting
A blade is cut out from a stainless steel material with a laser beam controlled by a computer program. Precision laser cutting, rather than presswork, is used for the high-grade 7000-model scissors as they have a fine latching structure on the blade for the scissors handle to be firmly fixed to the blade.
Thermal process
The laser-cut blade is brought into an electric furnace heated to about 1,000ºC. Then, it is cooled down in water to cause a change in the structure of the steel material, which results in a harder blade. In addition, annealing the blade at 180ºC gives it tenacity as well as hardness.
Rear grinding / Surface polishing
The rear of the blade is pressed against a high-speed rotating abrasive belt to shape the side of the blade along its periphery. Then, the blade surface is polished to make it look beautiful.
Creating a back clearance / Blade edging
The inside of the blade is ground to create a back clearance, or a slight depression in the center of the blade, which is characteristic of high-grade scissors and designed for the applied force to concentrate on the blade edge. Once the back clearance is created, the edge of the blade is sharpened with a grinder.
Shot blasting
Shot blasting is a process in which glass beads (particles of glass) are pneumatically shot against the blade at high speed to grind its surface. A surface area hit by a glass bead is slightly scraped off, with a tiny hollow left in the area. A shot-blasted blade has a lusterless, ground surface, which gives the scissors a quality appearance.
Handle molding
The handle part is molded by pouring the heated resin into molds set with the blade.
The fine groove is designed by laser cutting in the handle part of the blade for tightly connecting resin with the blade. This prevents the handle from being detached even grasping.
Marking
The logo and product name are marked by irradiating laser light on the blade. This is the application of the characteristics that heating the material in the air makes the surface to be oxidized and black. The design of marking is controlled by a computer, and precisely printed on the blade.
Blade tip edging
The tip part of the blade is sharply grinded with whetstone. The blade edges are completed to be sharp. Although the burrs (ragged edges formed during grinding) can be seen on the blade edge after grinding, the blade edge is completed by thoroughly removing the burrs at the final process.
Bending / Fastening screws(Assembling)
Two blades which became sharp by blade tip edging are fastened with screws, and the gap between two blades is adjusted by slightly bending the blades inside. Then, the contact of two blades is finely adjusted while checking opening and closing force and sharpness. Finally, two blades are adjusted to be exactly aligned by grinding the tip of scissors. This work is called edge adjustment.
Adjustment / Inspection / Packaging
All scissors are finally checked for sharpness. The inspection is carried out for checking sharpness of them manually by cutting the piled eight clothes with them. The scissors that pass these adjustment and inspection are packed after proper care.
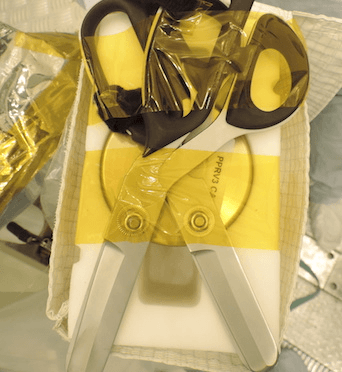
KAI's scissors, utilized also in outer space
KAI's scissors, appreciated at home and abroad, are utilized also in outer space. KAI, commissioned by an American company, has developed scissors that are suitable for the usage in outer space. At the present day, these scissors are utilized for works in the International Space Station. They are special scissors that have rounded ends to prevent them from sticking in astronauts or machinery by mistake.