PROCESSRAZOR
カミソリの製造工程
プレス
カミソリの材料となるステンレス刃物鋼をプレス機で加工する。ステンレスは材料を錆び難くするクロムのほか、刃体を硬くするカーボンが数%含まれている。材料の厚みは0.1mmほど。テープ状になった材料を巻出し、プレス機で穴を開けた後、また元のようにテープ状に巻き取られる。1分間に500枚以上のカミソリ刃が打ち抜かれる。
熱処理
プレス工程を終えた時点では、まだステンレス鋼はグニャグニャと曲がる状態のまま。そこで、約1000度の電気炉の中で加熱し、その後急速に冷却することで焼きが入り硬くなる。そして、更に-80度程度に冷やすことで硬さを増し、それをもう一度再加熱することで、見た目は加工前とまったく変わらないものの、粘りが出て、折れにくい鋼材が完成する。
刃付
焼入れした材料の端面に砥石による研削によって、刃先を形成することを「刃を付ける」と言う。刃を付ける工程は、最初に粗めの砥石で削り、その次に、最初よりも少し鈍角に中程度の砥石で削っていく。最後に、さらに細かい砥粒の砥石で刃の最先端を削るという工程をたどる。薄い板状の鋼材に角度の鋭い刃を付けるのは、貝印の工場が積み重ねてきた長年のノウハウの詰まった技術である。
研磨
刃付の第三段階で最先端を削った部分にはバリ(研削時にできる金属の出っ張り。返しともいう)が付着している。これを牛の皮を使った特殊な皮砥で磨いていく。皮砥の種類や刃先へのあて方により、髭剃りに最適な刃先の形状をサブミクロンの精度で仕上げることで、繊細な切れ味を実現することができる。
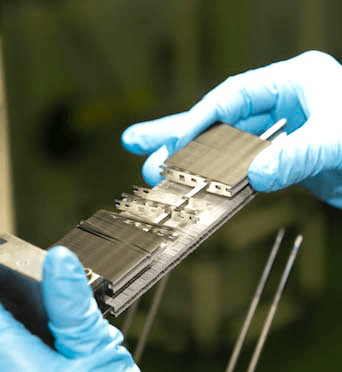
大量のカミソリ刃を全数検査できる秘密
串刺しになったカミソリの刃の束を見ると、不思議なことに墨を塗ったように黒く見える。これは刃の先が0.01μmまで鋭利になっているため、光を反射させるスペースがないからだ。逆に言うと、ここで光が反射するということは、それだけの鋭角を保てていないということになる。そのため、カミソリ刃の検品は蛍光灯に照らして目視で行なわれている。
検査(刃)
研磨されたカミソリの刃は、ここで初めて一枚一枚に分割され、串刺しにされた刃の束が出来上がっていく。背側はステンレスならではの光沢を持つが、逆の先端側は鋭利になっているため、光を反射することがなく、黒く見える。この時、少しでも光っていれば、刃先は鋭利な角度を保っておらず、不良品となる。こうした検査を目視で一枚一枚行なっていく。
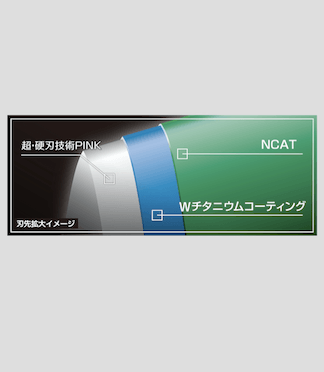
刃の耐久性を極限まで高める独自技術「PINK」
2008年に開発された独自の技術である「PINK」は、従来製品よりも刃先の硬度を70%アップさせる最新技術。PINK処理を行なってステンレスをより強靭にしてからコーティング工程を施すことで、極限まで切断抵抗を抑え、使用中に刃が欠けてしまうことを防ぐ。
コーティング・焼成
先端を極限まで鋭利にした刃を摩耗しにくくするために、硬い金属膜をコーティングする。これは刃先部分を錆びにくくする目的もある。刃が肌の上を滑りやすくするため、さらにフッ素樹脂をコーティング。その後、加熱をして樹脂を溶かし表面に成膜をする。このように、2層にコーティングすることで、カミソリとしての剃り味と耐久性が格段に向上する。
プラスチック成形
カミソリの持ち手になるハンドル部分のプラスチックは、加熱して溶けた樹脂を金型に流し込んで作られる。2色ハンドルの場合は、別々の樹脂を流し込み、同時に一本のハンドルに成形する。ベスティは、グリップ感を追求したゴム製の柔らかい樹脂がハンドル部分に使われているが、開発時に人間生活工学研究センターとの共同開発により取り入れられた技術である。
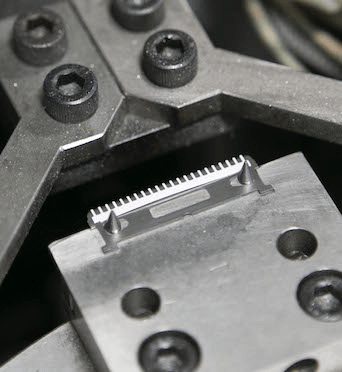
自社開発のカミソリ組立加工機
貝印の工場にあるカミソリの組立機は、ほぼ100%が社内で設計・製作されたもの。そうすることで、カミソリの進化に合わせて改良を加えることができ、新たなラインナップの製造にも柔軟に対応することが出来るほか、現場からの要望や評価を細かくスピーディに反映することが可能となる。
組立て(ヘッド)
上刃、下刃の2枚の刃の間に、厚さ0.5mmのアルミの板を挟み込み、上に「天」、下に「地」と呼ばれる樹脂パーツを組合せカミソリのヘッド部分が出来上がる。さらにスムーサーと呼ばれる、ヒゲ剃りの際に滑りをよくする水溶性の樹脂が取り付けられて完成。
組立て(ハンドル)
自社で製造したカミソリ組立機。パーツフィーダーと呼ばれる装置によって、振動を利用してハンドル部品を一定方向に並べていく。そこに組立の済んだカミソリヘッドが合流し、ひとつひとつ高速に組み立てられていく。
検査・包装
カミソリヘッドとハンドルが組み立てられ、一本のカミソリになると、ロボットによってコンベア上に並べられ袋に投入される。この時、組立機とコンベアの上に設置された各種センサーによって、刃の異常、樹脂部品の位置、組立精度など多くの検査が行なわれ、品質の高いカミソリが完成する。